Double Disc Dryer
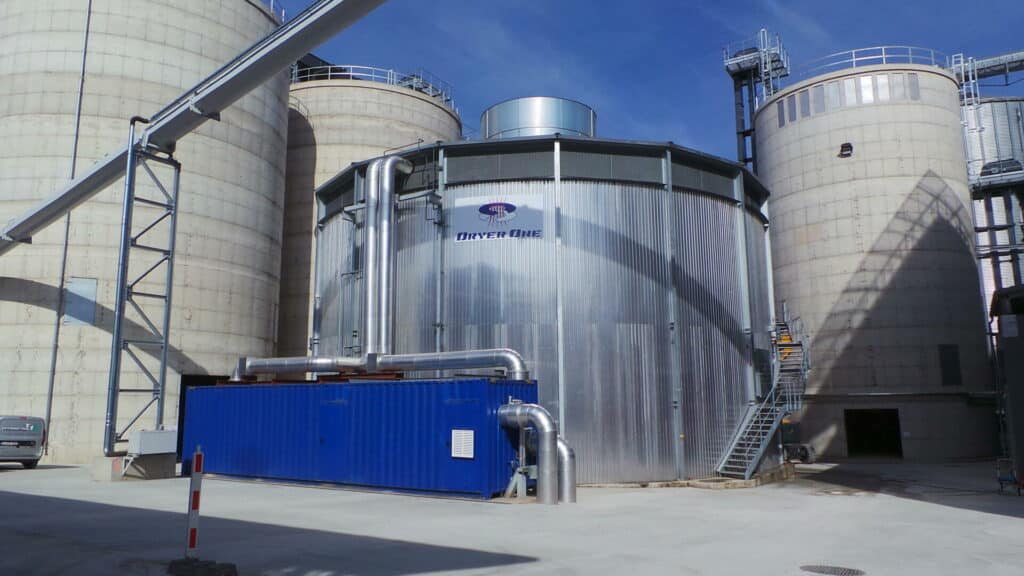
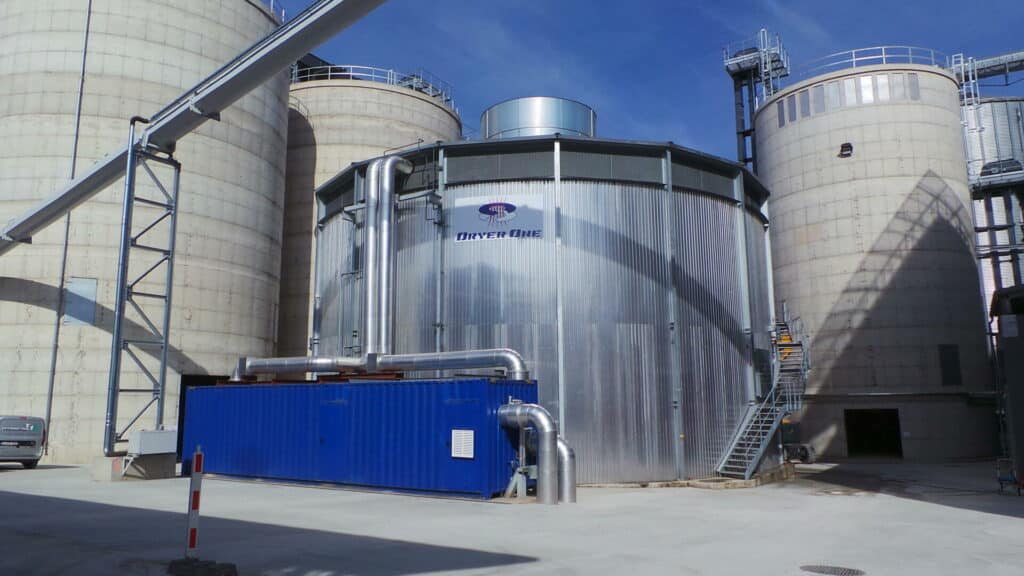
The Dryer One™ “Double Disc” Dryer combines thermal energy optimization with high-capacity production. The material to be dried is first spread over a lower rotating disc. After completing a full rotation, it is transferred to an upper rotating disc, which rotates in the opposite direction, completing the drying process.
Hot air (149 to 212 °F) from an external low-temperature energy source (such as cogeneration or a boiler) passes successively through the two discs from top to bottom. This process ensures uniform heat distribution and exceptional energy efficiency. After passing through the two beds, the used air, saturated with water and cooled to a temperature of 77 to 86 °F, is efficiently expelled through the central chimney.
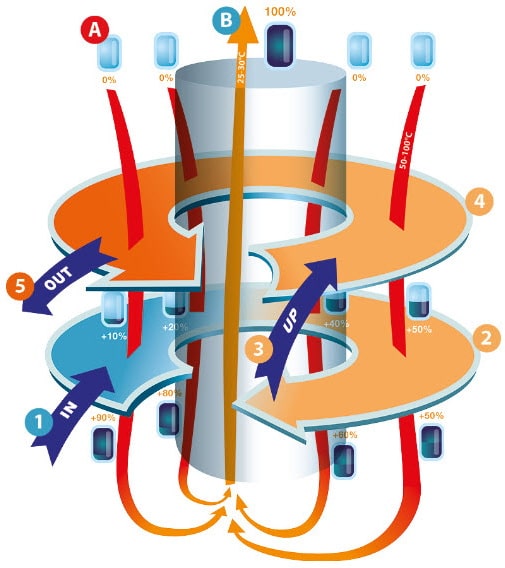
![]() |
IN The lower rotating platform is fed with material to be dried. |
![]() |
DRYING LOWER LEVEL The material to be dried completes a 360° rotation. |
UP The material to be dried is transferred to the upper rotating platform using a bucket elevator or a screw conveyor. |
|
DRYING UPPER LEVEL The material to be dried completes a 360° rotation on the upper rotating platform, moving in the opposite direction to the lower platform. This exclusive technology improves heat distribution and achieves higher efficiency than other hot-air drying techniques. |
|
OUT The dried material is discharged to the packaging or storage area. |
|
HOT AIR INLET Hot air is drawn from top to bottom, countercurrent. It successively passes through the upper and lower platforms. |
|
EXTRACTION & EXPULSION OF MOISTURE-SATURATED AIR Moisture-saturated air is pushed upward for expulsion. Any dust particles can be filtered. |
Double Disc Range
*Example of drying wood sawdust with a moisture content of 10%.
These values are provided for reference only and may vary depending on the nature of the product and drying conditions.
Exclusive Advantages and Features
The two layers of material are successively traversed by the same flow of hot air. After passing through the first (upper) disc, the air retains a residual amount of thermal energy, which can be reused to preheat the material on the lower disc. Once it has passed through both layers, the used air, fully saturated with water and cooled to a temperature of 77 to 86°F, is expelled through the central chimney.
In addition, the dryer’s outer casing is fully insulated to optimize the device’s energy performance.
Dried materials processed at low temperatures generate extremely low levels of pollutant particles. Additionally, the lower disc, which holds the wet material, captures dust particles that may fall from the upper (dry) disc.
An integrated fire detection and suppression system, combined with the use of primarily non-flammable materials that prevent fire spread, makes the Dryer One™ a piece of equipment with an extremely low fire risk, enhancing the safety of the production site.
The circular design of the Dryer One™ minimizes its footprint, allowing easy integration into existing production sites.
The advanced automation system of Dryer One™ optimizes efficiency, precision, and safety. Fully automated, it requires minimal operator supervision, ensures precise control of moisture levels, and enables the generation of production reports.
Dryer One™ dryers are compatible with various low-temperature heat sources, such as hot water, hot air, or steam, produced by biomass boilers, natural gas burners, or cogeneration systems.